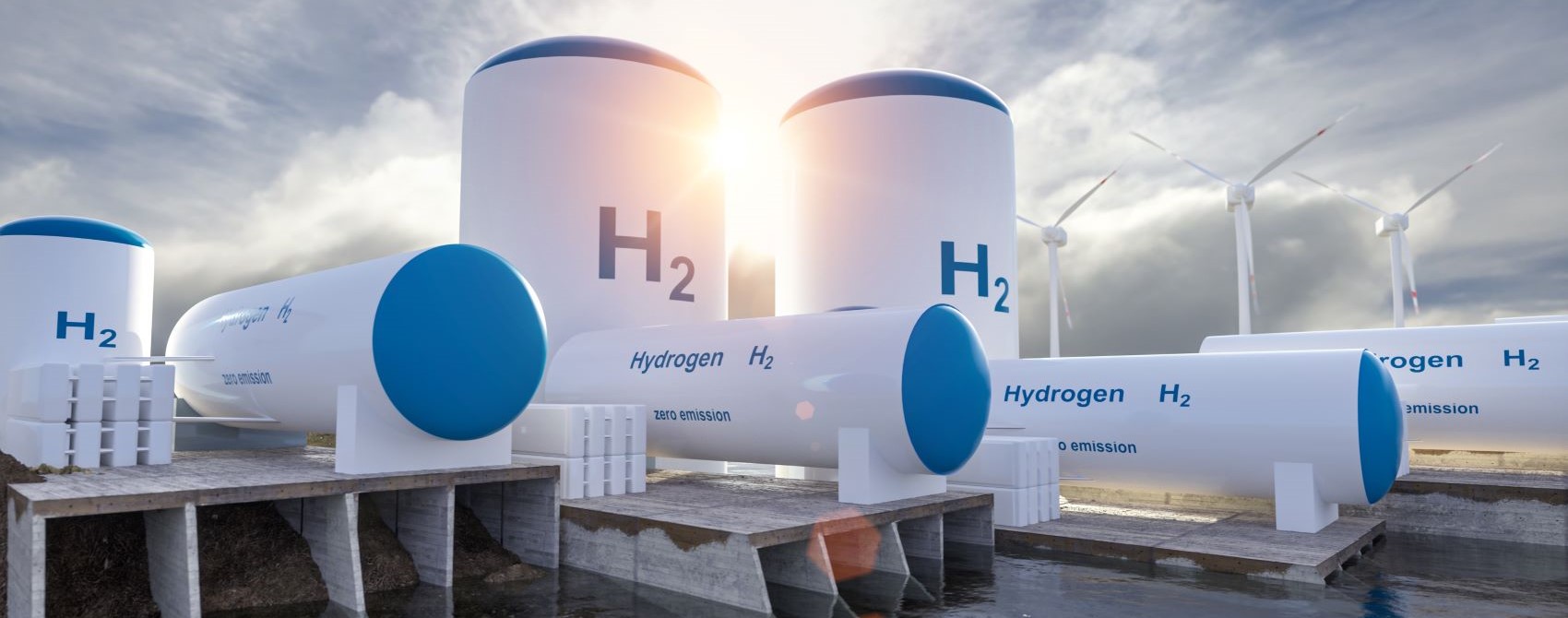
Leak Testing Hydrogen Fuel Cells, Hydrogen Storage Tanks, and Components
Hydrogen as clean, alternative energy is an evolving industry with promising capabilities in a variety of industries, including modes of transport like hydrogen fuel automobiles, trains, ships, and planes, as well as industrial factory environments with high energy consumption like those producing concrete, iron, castings, and more.
There are many components involved with hydrogen energy that must be leak tested including hydrogen fuel cell leak detection, leak testing of hydrogen tanks, and testing hydrogen refueling systems, pipes, valves, and more. Leak testing hydrogen components poses a challenge, as hydrogen can be a very dangerous gas if it leaks, and it can leak through extremely small cracks. Even a slight concentration and mixture with oxygen can cause hydrogen to be flammable and explosive, so it is extremely important to ensure an accurate, reliable leak test designed to catch even the smallest leaks during the manufacturing process.
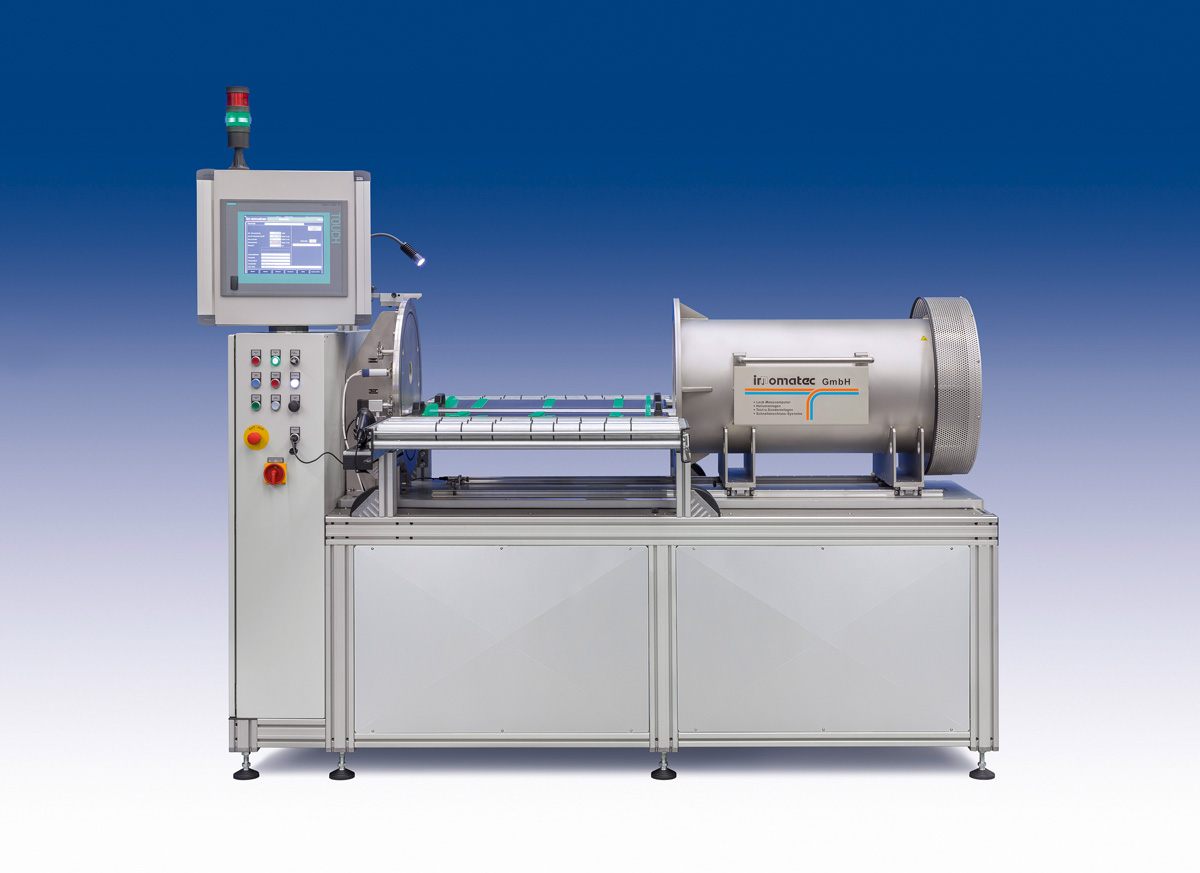
Methods Of Hydrogen Leak Detection
Tracer Gas Testing
Components that will have direct contact with hydrogen must be tested with tracer gas or helium leak testing methods. This is because we must test to leak rates that are so small that air leak test methods will often not be able to conduct the test. In this case, most manufacturers will use a tracer gas leak test method, commonly using helium, a helium mixture, or a forming gas mixture of hydrogen and nitrogen.
These components include those involved in building a hydrogen fuel cell, or hydrogen battery, including the bipolar plates and cooling channels, as well as the supporting components like piping, pressure regulators, valves, storage tanks, and all these kinds of components which actually run the hydrogen to and from the tank need to be tested with tracer gas to ensure they are leak-tight. These parts and components need to be tested at or above operating pressure to ensure safe functioning and product quality, leak testing up to 875 bar as a standard, and even higher pressures if needed.
Air Leak Testing
Components that won’t have direct contact with hydrogen can be tested using air leak testing. This includes electrical components, housings, cooling systems, exhaust systems, or blowing systems, cables, and plugs. These components may need to be water-tight, or steam-tight, etc., but they don’t need to be tested for the potential of a hydrogen leak.
If it is an applicable application, using air leak testing methods, such as pressure differential testing or mass flow testing, can provide a more cost-effective option than testing with tracer gas or helium—but only for components that are not directly in contact with hydrogen as a gas or as a liquid gas.
In some cases, a combination of tracer gas and air leak testing methods may be used, especially when testing assemblies that feature different types of components.
Leak Testing Standards and Specifications for Hydrogen Components
As the use of hydrogen in products continues to evolve, so do the leak test requirements and safety standards. Currently, manufacturer/OEM requirements are often based on experience, theoretical calculations, or empirical tests and long-term studies on prototype parts. Standards that currently apply to hydrogen testing applications include:
- ISO 19880-1
- ASME B31.12
- CSA B51
- DIN EN 1713
- VDI/VDE 2887
It is important to note that the requirements for leak testing hydrogen components may vary depending on the application and country. Therefore, it is advisable to consult the specific national and international standards that apply to your region and project. Local regulations and laws may also specify additional requirements for testing of hydrogen components.
innomatec can help you identify the specifications required for your test and design a solution to deliver an accurate, reliable leak test that complies with the applicable standards.
Below you can see an example of a system that is used for hydrogen components designed to meet the customer's requirements for leak testing and automation.
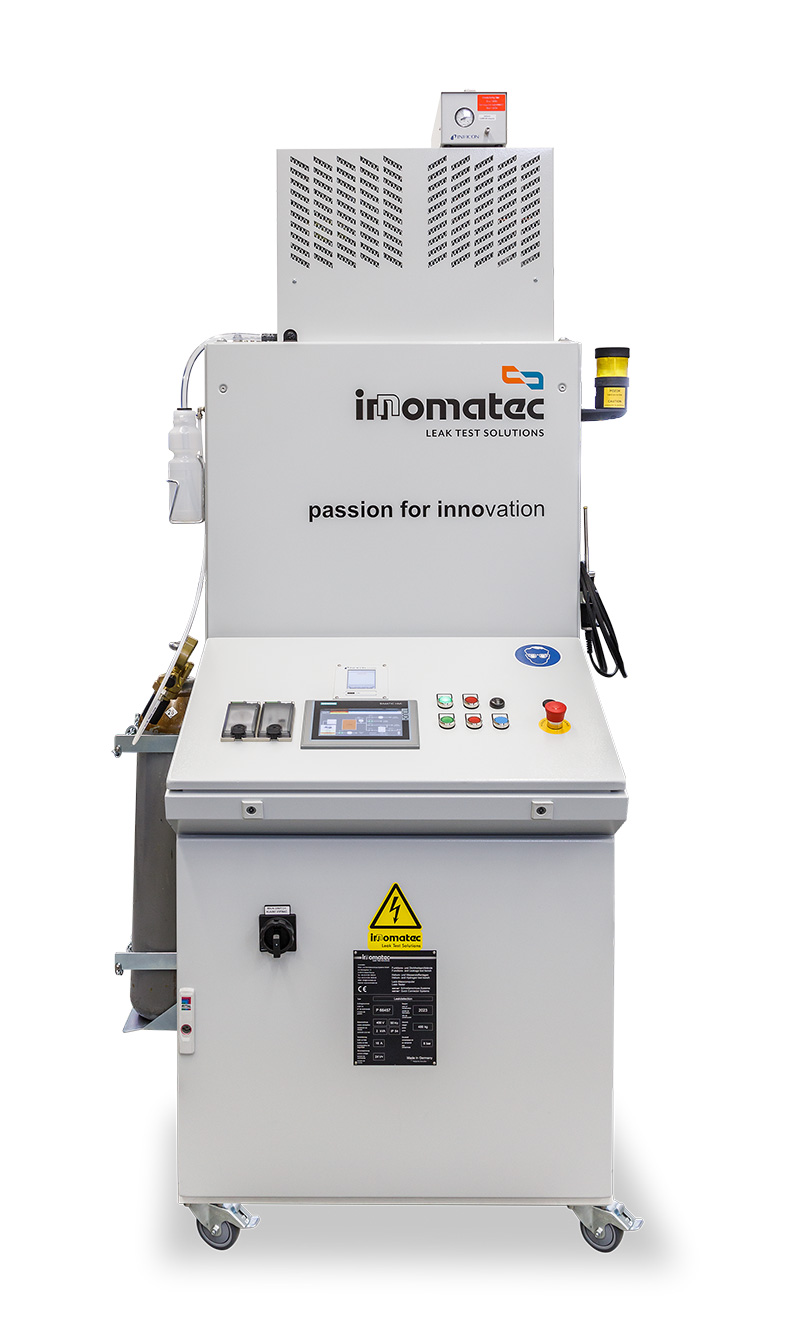
MHLS – Mobile Helium Leak Test System: for manual leak detection of H2 assemblies like fuel cells, Vehicles, Refueling stations, etc.
- Bipolar plates
- Connectors
- Cooling channels
- Hydrogen fuel cells / batteries
- Hydrogen refueling systems
- Hydrogen storage tanks
- Pipes
- Pressure regulators
- Valves
innomatec Solutions for Leak Testing Hydrogen Components
Using hydrogen as an alternative energy source is an evolving topic, and as such are the leak test standards and best practices. However, with over 40 years’ experience, innomatec is positioned at the forefront of hydrogen fuel cell testing and testing of hydrogen components, staying up-to-date on the latest hydrogen fuel cell technology as this industry continues to evolve. Our engineers will work with your team to help you understand the testing requirements for your applications and design testing solutions that ensure a safe, high-quality product.