Closed Component Method
The closed component, or dosing, method (D) is used for completely closed components that cannot be exposed to test gas via an opening, e.g., watches, cell phones, control units, etc. It is also used for the testing of components that cannot be exposed to test gas via an opening.
The completely closed test specimen is placed in a measuring chamber (bell) which is then closed.
This measuring chamber is not directly pressurized with positive or negative pressure but is dosed via a previously evacuated or filled pre-volume.
The volume between the test specimen and the measuring chamber is known, so that a defined pressure ratio is expected.
Any leakage in the test specimen changes this ratio and thus leads to a change in pressure, which is recorded and evaluated by means of a pressure transducer (A) or pressure difference sensor (R).
The principle of the dosing method can also be integrated into other measuring methods in order to perform a volume determination, a component interrogation or an exact gas quantity determination.
The following standard measuring methods with the dosing principle are available:
Closed component method with pressure change method DA
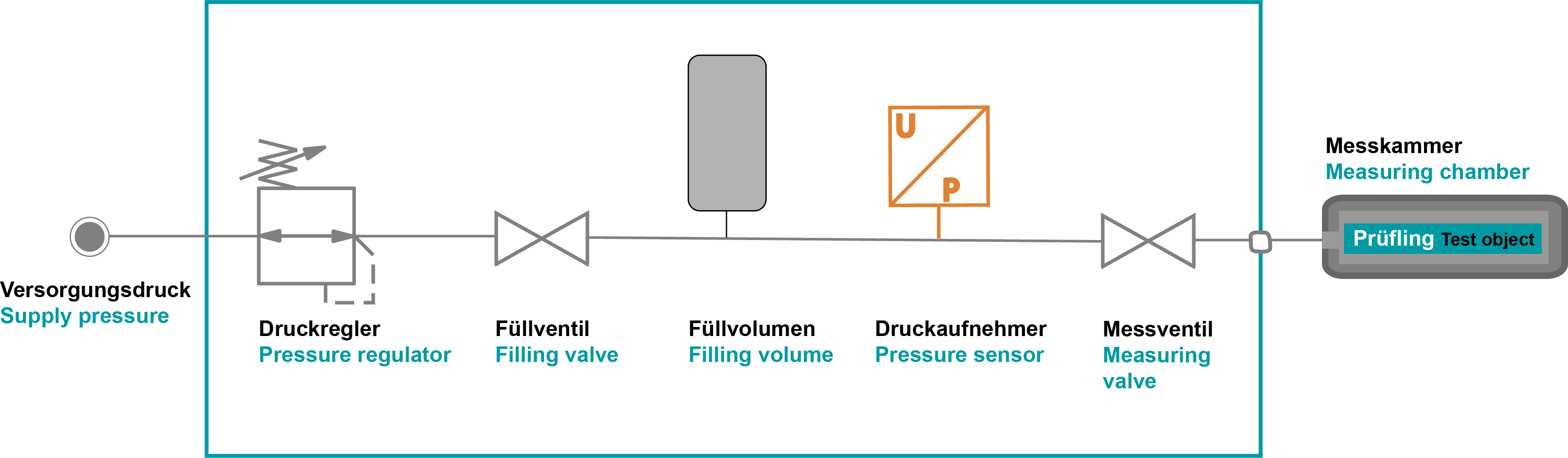
Closed component method with pressure differential method DR
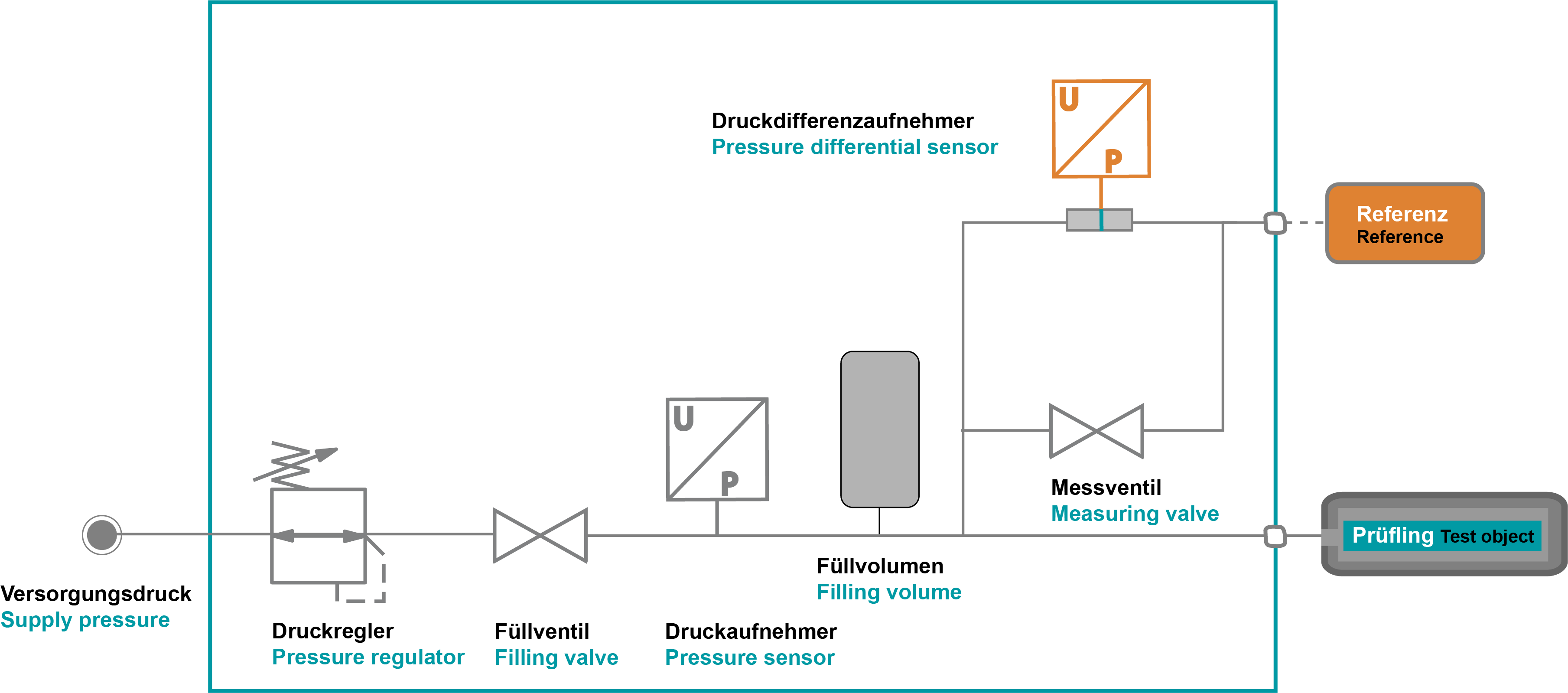
Volume determination
As an alternative to the dosing method, the volume determination (C) is used to determine the volume of the test specimen. It offers the same pros and cons as the closed component approach.
A known pre-volume is filled or evacuated with a known test pressure and then expanded in the test specimen. The volume of the test specimen is determined with the resulting pressure.
The principle of volume determination can also be integrated into other measurement methods.
Test medium:
Compressed air/vacuum or nitrogen
Detectable leak rates:
Volume and pressure dependent > 1 cm3 / min
Detectable volume differences:
2-3% of the measuring volume, depending on the internal volume of the component
Method:
A known pre-fill volume is pressurized/vacuumed and stabilized. This gas volume is then fed into the test specimen or into the test specimen chamber. The resulting pressure is a measure of the volume and is used to detect coarse leaks. The additional pressure change caused by leakage is measured and evaluated.
Advantages:
- Simple and inexpensive method
- Volume determination, testing of closed parts possible if they have a free internal volume which is not less than approx. 10% of the free chamber volume.
- Standard method for waterproof consumer goods
Disadvantages:
- Relatively long Test duration
- Pressure shocks are possible due to the procedure