Flow Test Method
This method is used when a test item is not closed, and its continuity must be tested for volume.
Via a precision pressure controller or a precision flow controller, either the pressure or the flow is constantly adjusted in the test item, so that the volume flow or the pressure at the inlet of the test item can be measured.
Since the measured value is evaluated directly by the sensor and output in a leakage rate, the actual measurement can take place directly after filling. A stabilization phase as with pressure change measurements is not required.
Alternatively, a flow measurement can also be carried out using the dynamic pressure method. In this case, it is not the flow that is measured, but the change in test pressure when the cross-section is tapered or expanded.
Particularly in the automotive sector, dynamic pressure tests are often used to determine partial closures, e.g., > 30%.
Combinations of the methods are also possible, e.g., for testing pressure control valves or functions of Venturi nozzles.
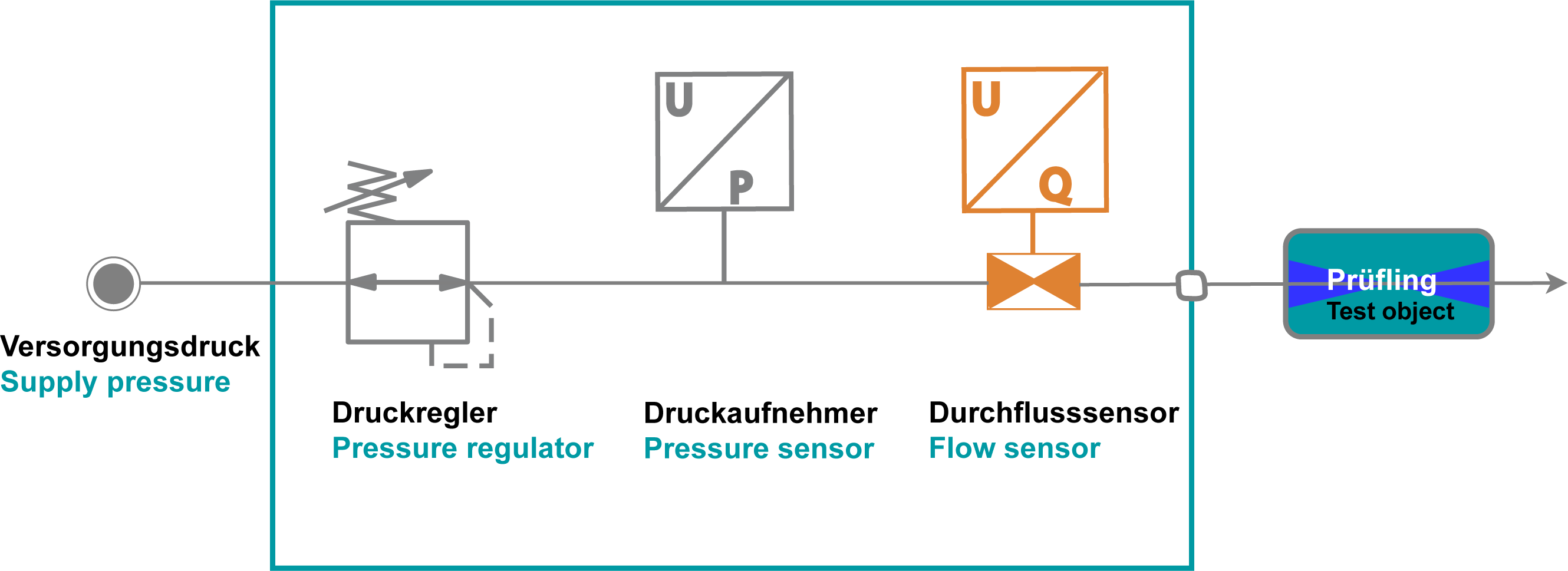
Test medium:
Compressed air, nitrogen, special versions for water, others on request
Test pressures:
In different measuring ranges, stepless from 0.1 - 10 bar
Flow measuring range:
1.5 - 50 ml/min, resolution 0.5 ml/min with high performance resolution Flow ranges up to 400 l/min, special version also higher
Method:
Flow measurement is carried out using either a thermal mass flow or laminar flow element. The dynamic pressure measurement identifies blockages in the component caused by accumulating gas. This allows a production error to be detected very quickly and effectively. Even complex components with several openings can be specifically checked. Flow measurement is one of the fastest measurement methods with air and can usually be realized in a cycle time of less than 5 sec.
Advantages:
- Short test times
- Volume independent of test volume
- Easy commissioning
Disadvantages:
- High costs
- Less robust against contamination