Manual Leak Detection Using Trace Gas
Manual leak detection using trace gas can be used to find and determine the size of leaks in components. The test specimen itself is filled with a trace gas (usually helium or forming gas). After a mixing phase, if any, the test specimen can be inspected at prominent points or over the entire surface with a sniffer probe manually guided by the worker.
Leakage is indicated directly as a leakage rate via a display and/or acoustically. Test systems that work according to the accumulation or vacuum integral method are ideal for leak detection using trace gas, as most of the hardware is already available. In contrast to leak detection spray, this method does not contaminate the component with soapy water.
In test facilities, the sniffer probe is also often used to check for possible leaks within the facility, such as the trace gas cylinder bundle.
This test method applies in particular to expensive parts and assemblies in whose manufacture you have already invested a lot and whose scrapping is out of the question.
Manual leak detection makes it possible to find leaks, and is usually used for troubleshooting as well as process optimization
Test medium:
Helium, helium mixture (air or nitrogen), forming gas (5% H / 95% N)
Test pressures:
Stepless from 0.01 - 16 bar
Detectable leak rates:
Volume and component dependent < 1 x 10-5 mbar*l/sec (in industrial environment)
Method:
The test item is filled with a trace gas or trace gas mixture and the gas escaping through a possible leak is analyzed via a sniffer probe and leak detector.
Advantages:
- Low investment costs (depending on manual vs. automated requirements).
- Single leak rate detection
- Exact detection of leak position
- Not dependent on ambient and component temperature
- Not dependent on the stability of the test specimen (small volume changes, vibrations, etc.)
- No component contamination. e.g., by leak detection spray
Disadvantages:
- Handling of inert gas required
- Higher costs for fixtures and test stand (compared to air testing)
- Cleaning system for "contaminated environment" required (room ventilation)
- Longer cycle time
- Manual handling; high operator costs; not fail-safe
- Only partial detection (weld/adhesive seam), full-surface detection requires very long time
- Measuring results depend on measuring distance and operator care
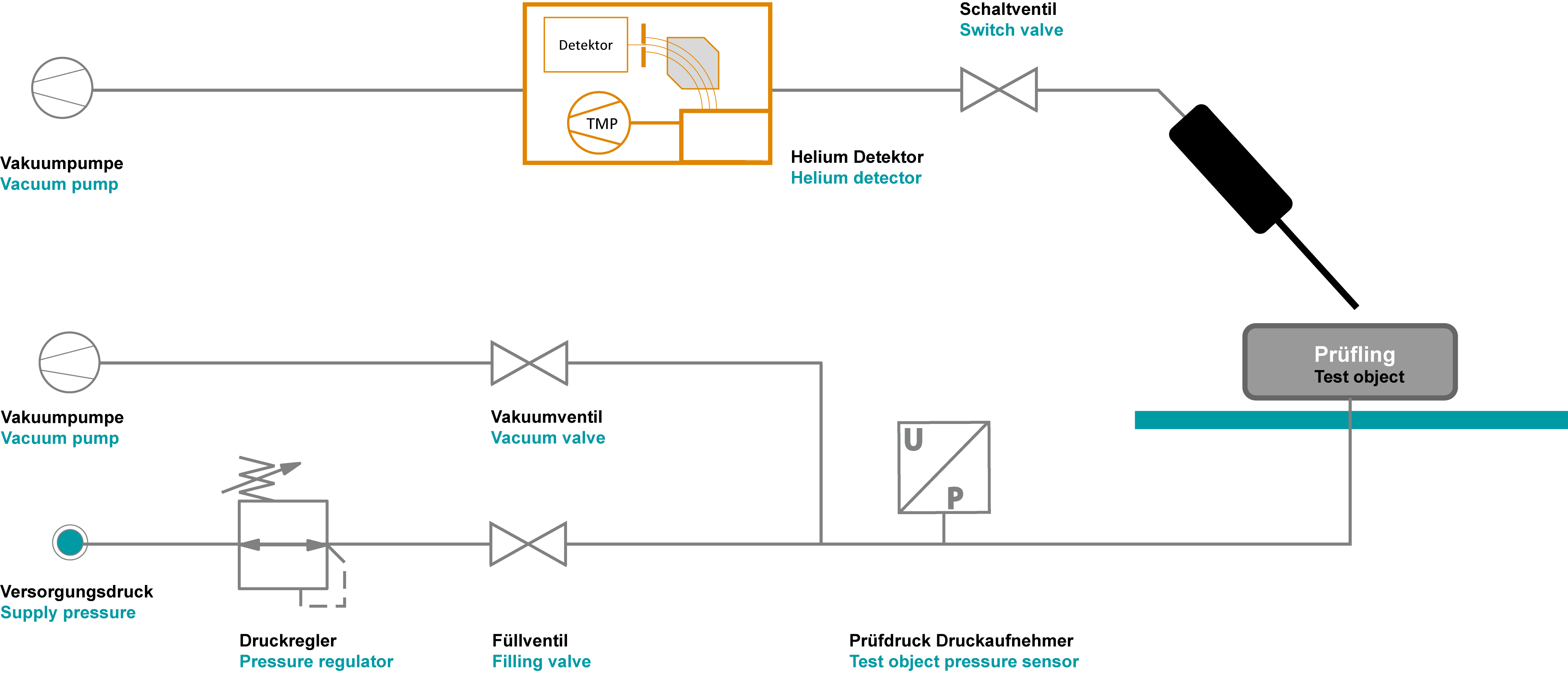
Robot-guided Sniffer Leak Detection
Robot-guided leak detection is a further development of manual leak detection and is based on the same technical principles. In this case, the helium "sniffing" test is applied automatically with a sniffing robot for more complex applications.
The constantly adjustable speed and distance to the test item, as well as the special precision, enable fast and accurate measurement results in leak detection. Test pieces that have already reached a high production rate or are easy to rework can be specifically sealed by leak detection.
This type of leak detection can be used as a downstream process to a leak test of the total leakage rate, or as a stand-alone process. A distinction is made between focusing on the exact positional accuracy and leak size (leakage assessment) or rapid leakage detection (position and IO/NIO assessment).
Leakage evaluation: Due to very constant distance and travel speed monitoring, as well as a high sampling rate, individual leakages can be evaluated very precisely. By means of the stored parameters, the machine decides whether an individual leakage needs to be reworked or not.
Leak detection: If the actual inspection is carried out using a total leakage rate (one value for the entire test item), leak detection is usually only used to find the position for the subsequent reworking process.
The good/bad evaluation is not carried out by the leak location, but by the actual leak testing machine.
When high positional accuracy and reproducible leak detection results are required, robot-guided leak detection is the measure of all things.
Test medium:
Helium, helium mixture (air or nitrogen), forming gas (5% H / 95% N).
Test pressures:
Stepless from 0.01 - 1,000 bar
Detectable leak rates:
Volume and component dependent < 1 x 10-5 mbar*l/sec (in industrial environment).
Method:
The test item is filled with a trace gas or trace gas mixture and the gas escaping through a possible leak is analyzed via a sniffer probe and leak detector. The results can be displayed to the operator via a screen on the tester.
Advantages:
- Low investment costs (depending on manual vs. automated requirements).
- Single leak rate detection
- Very accurate detection of leak position
- Not dependent on all environmental conditions (temperature, etc.)
- Not dependent on the stability of the test item (small volume changes, vibrations, etc.)
- No component contamination. e.g., by leak detection spray
Disadvantages:
- Handling of inert gas required
- Higher costs for fixtures and test stand
- Cleaning system for "contaminated environment
- Only partial detection (weld/adhesive seam), full-surface detection takes a very long time
- Measurement results dependent on measurement distance and gas concentration