Precise testing systems for valves & fittings - flexible & reliable.
Test benches and machines for leakage and functional testing of valves and fittings
Leak testing and functional testing procedures are a very important part of the manufacturing process for valves, fittings, and faucets—however, the design of these machines can be complex and challenging for manufacturers.
Many manufacturers must address high product diversity with hundreds of test item variants, all requiring different fixturing and sealing, leak rates, and pressure specifications for testing. Functional testing is also often required, such as diaphragm tests, valve movements, check valves, pre-setting, latching test or spring forces. The challenge is in accommodating all of these different tests and procedures in one, safe and efficient machine.
With over 40 years’ experience serving manufacturers, innomatec has developed clever solutions that allow for the most efficient and accurate testing of valves and fittings, with manual and automated solutions that make fixturing and sealing as simple as possible, even when testing multiple part variants on one machine.
Contact us to create a plan for your leak testing and ensure optimal performance of your valves and fittings. Our team will ensure your line is compliant with any regulatory requirements, and ensure the most accurate, safe, efficient test process for your needs.
Flexible and customized machine concepts for multiple tests and designs in a single system
Many tests must be performing on valves and fittings to ensure they meet product quality requirements. These tests include potentially various types of leak tests, as well as a wide variety of functional testing. Many times, these tests are all combined in one machine, for ease of process. For example, a valve or fitting could first undergo an internal and external leak test(s) (using helium, air, nitrogen, etc.), followed by a flow test, membrane test, valve seat jogging (motion test), latching test, backpressure test, and more.
Many valve and fitting manufacturers also often produce many different models and variants of these products. Depending on the number of different parts and the level of throughput, having a different machine to test each part would be quite inefficient and costly. To make this manufacturing process more efficient and cost-effective, innomatec designs solutions that allow manufacturers to test many different variants of parts using ONE machine, and combine tests so that leak testing and function tests can all be accomplished as part of the same process. Our systems are designed in such a way that they require as few replacement parts as possible - ideally none at all. This reduces both the initial investment costs and the running costs, as fewer wearing parts need to be replaced. The ability to combine different tests and test many part variants with one machine ultimately optimizes the investments in tooling, which can be substantial.
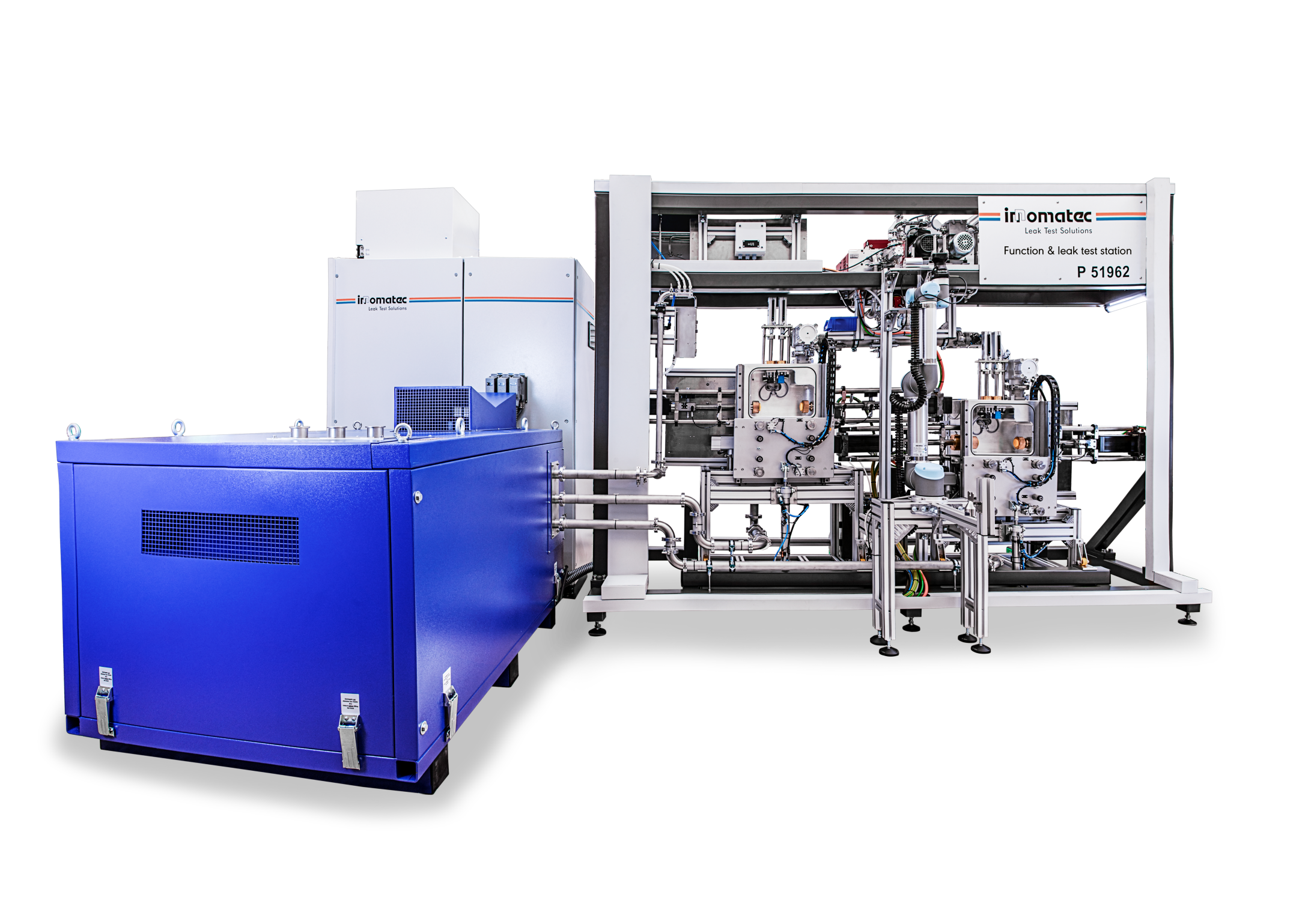
Manual and automated valve leak testing solutions
Valves and fittings can be leak tested using manual or automated methods. The best option will depend on a variety of factors, including throughput goals, the number of different product types, availability of human operators to load the systems, budget, and more.
For example, when manufacturing a simple one-way valve, a manually-loaded leak test solution may be preferred. innomatec would design a manual test solution made to ensure operator safety (CE certified). All manual test station solutions are designed with various features to ensure the highest operator well-being and safety, including ergonomic design, closed-door systems for high-pressure valves, open-door setups for low-pressure valves, and more.
If your line has a large quantity of parts and variants, and/or want to reduce the reliance on human operators, an automated / robotic leak test solution would be a better fit. An automated leak test solution for valves and fitting boosts efficiency, simplifies fixturing and operation requirements, and often provides the most accurate test results. Automated solutions can include different feeding methods such as robotic handling with changing grippers, servo motor driven positioning and tooling, or a light table with camera positioning.
Flexible machine designs for nearly any industry or application
Many different industries rely on valves and fittings including, plumbing (faucets, mixer valves, etc.), refrigerants, HVAC (heating systems), automotive (fueling systems, etc.), food processing, flow cells, and more. Testing requirements will differ based on the materials, design, and requirements of these specific parts and applications in the field. A variety of different leak test methods can be used, though the majority of leak test applications utilize either helium or air leak test methods—both well-served using the power and flexibility of the LTC-802 or LTC-902, depending on your needs.
For applications with very low, strict leak rates, like those found in the food processing industry and gas / refrigerant applications, helium is often the best option for leak detection. For applications testing larger leak rates, like plumbing and other water/liquid-based leaks, air leak testing methods are often sufficient. These tests can then be combined on one machine as needed, along with functional tests and assembly verification. innomatec is experienced in designing efficient and seamless leak and function testing solutions to meet any of your needs, regardless of complexity.
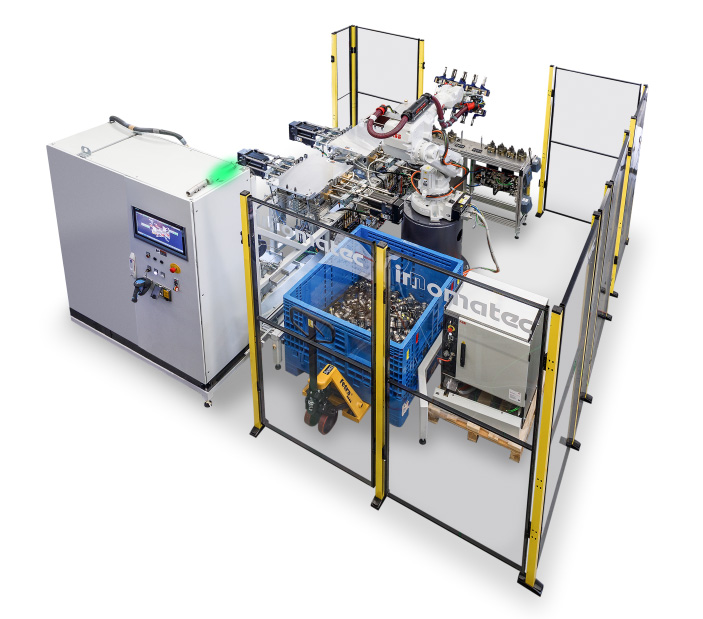
Test Method: Helium – Vacuum Integral Method
Special Feature: Automated loading and unloading by robots, minimal use of interchangeable parts, and precise OK rejection thanks to ultrasonic sensors. Ideal for efficient leak testing with high accuracy.

Test Method: Air: Flow Method & Helium Accumulation Method
Special Feature: Tests thousands of test piece variants with high-pressure safety. Optimizes functional testing and ensures precise results under various conditions.
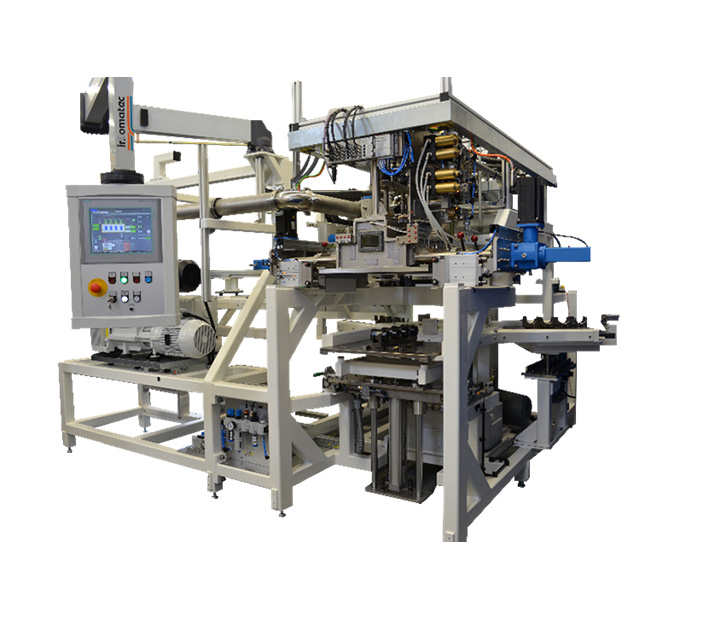
Test Method: Helium – Vacuum Integral Method
Special Feature: Testing of over 500 variants, including T-pieces, flanges, plugs, and connectors. Automatic loading optimizes the testing process and reduces manual effort.
Technical Specifications
LEAK TEST TYPES:
- Pressure leak testing
- Closed component leak testing
- Mass flow leak testing
- Vacuum testing leak testing
- Helium / tracer gas leak testing
TEST PRESSURES:
- Can accommodate low- and high-pressure testing (From vacuum up to pressures up to 1000 Bar / 15,000 PSI)
FUNCTION TEST TYPES:
- Membrane test
- Valve seat jogging (motion test)
- Pre-setting test
- Latching test
- Spring force test
- Backpressure test
- And more!
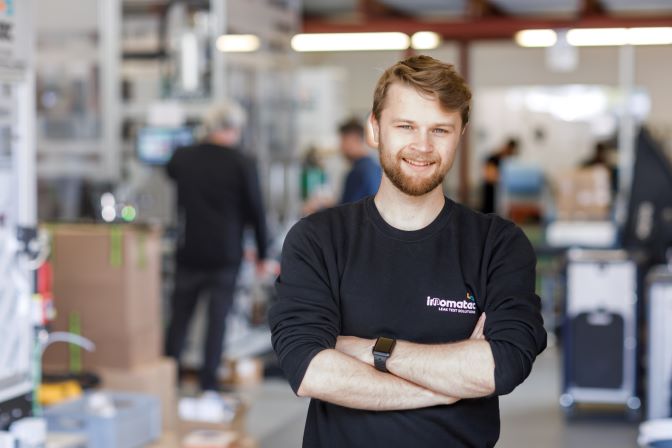
Consult the leak test experts—a team you can trust!
innomatec has over 40 years’ experience in the field of leak detection for valves and fittings. Our solutions are proven and trusted, featured on thousands of assembly lines across the globe.
Contact us today to make an appointment to discuss your leak test! Our leak test experts are ready to meet with you, learn about your application, and answer any questions you may have to ensure your team gets the best test solution for your needs.