Vacuum Integral Method
Test items that are tested by means of the vacuum integral method can be inspected for even the smallest leaks and bad parts can be removed from the production process.
A vacuum chamber and the fine vacuum created in it (~1x10-4 bar) form a very neutral measuring environment, which means that even the smallest leaks can be detected in the shortest possible time under very high test pressures for leak testing using track gas and leak detectors.
During the evacuation phase of the vacuum chamber, the test item itself is checked for coarse leaks, which prevents possible contamination with trace gas and the resulting cycle time extensions.
During the actual leak test, the amount of escaping trace gas, usually helium, but also forming gas and argon, inside the vacuum chamber is analyzed and output in a leak rate.
Depending on the test specification, pure trace gases or mixtures of air/nitrogen and trace gas can be used. This reduces the gas costs and thus the test costs per component.
Often the cost of test gases can be significantly reduced by using customized recovery systems and compressor units.
No other measurement method combines this precision with the shortest cycle times and the possibility of use in an industrial environment. For example, it is applicable for battery housings, coolant lines, coolant compressors or inverter housings, among others.
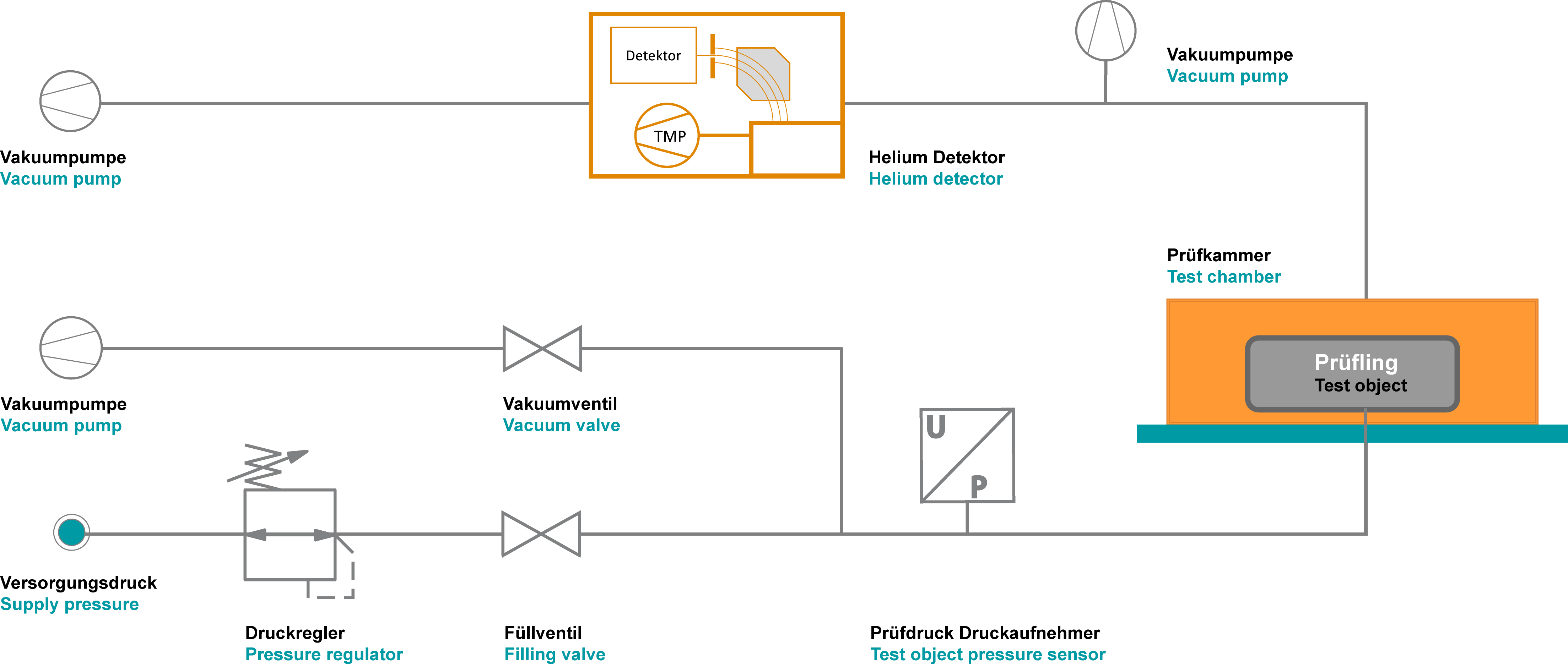
The vacuum integral method is particularly suitable for detecting very small leaks on components, sometimes at very high test pressures.
Test medium:
Helium, helium mixture (air or nitrogen), forming gas (5% H / 95% N)
Test pressures:
Stepless from 0.01 - 1,000 bar
Detectable leak rates:
Volume and component dependent < 1 x 10-9 mbar*l/sec (in industrial environment).
Method:
The test item is filled with a trace gas or trace gas mixture and the gas escaping due to a possible leakage is evaluated via a leak detector, inside the vacuum chamber. Due to the vacuum atmosphere in the analysis room, a very high accuracy and speed is achieved.
Advantages:
- Detection of a single leak rate
- Component volume only influences media consumption, not relevant to measurement
- Not dependent on all environmental conditions
- Not dependent on the stability of the test specimen (small volume changes, vibrations, etc.)
- Smallest leak rates can be detected
- Short cycle time, which can be adapted to the process by the design of the test stand
- Worker independent assessment
Disadvantages:
- Handling of inert gas required
- Highest investment costs
- High fixture and test rig costs (compared to air or accumulation tests, can be compensated by faster cycle time and higher machine availability)
- No localization of the leak