Pressure Increase Test Method
The pressure-increase method is characterized by the possibility of testing with very high test pressures of up to 1,000 bar. But this measuring system also offers considerable cycle time advantages for geometrically simple components with a large volume.
As with the pressure-increase method, the test specimen is pressurized and adjusted in absolute or relative terms to the ambient pressure.
The actual measurement takes place in a measuring chamber (bell) located around the test item. Any leakage in the test item leads to a pressure change within this chamber, which is recorded and evaluated by means of a pressure transducer.
The output of the measurement result can be given as a pressure change or as a leakage rate.
The possibility of being able to test specimens at very high pressures with very short cycle times at the same time makes the pressure rise method a good alternative to trace gas methods.
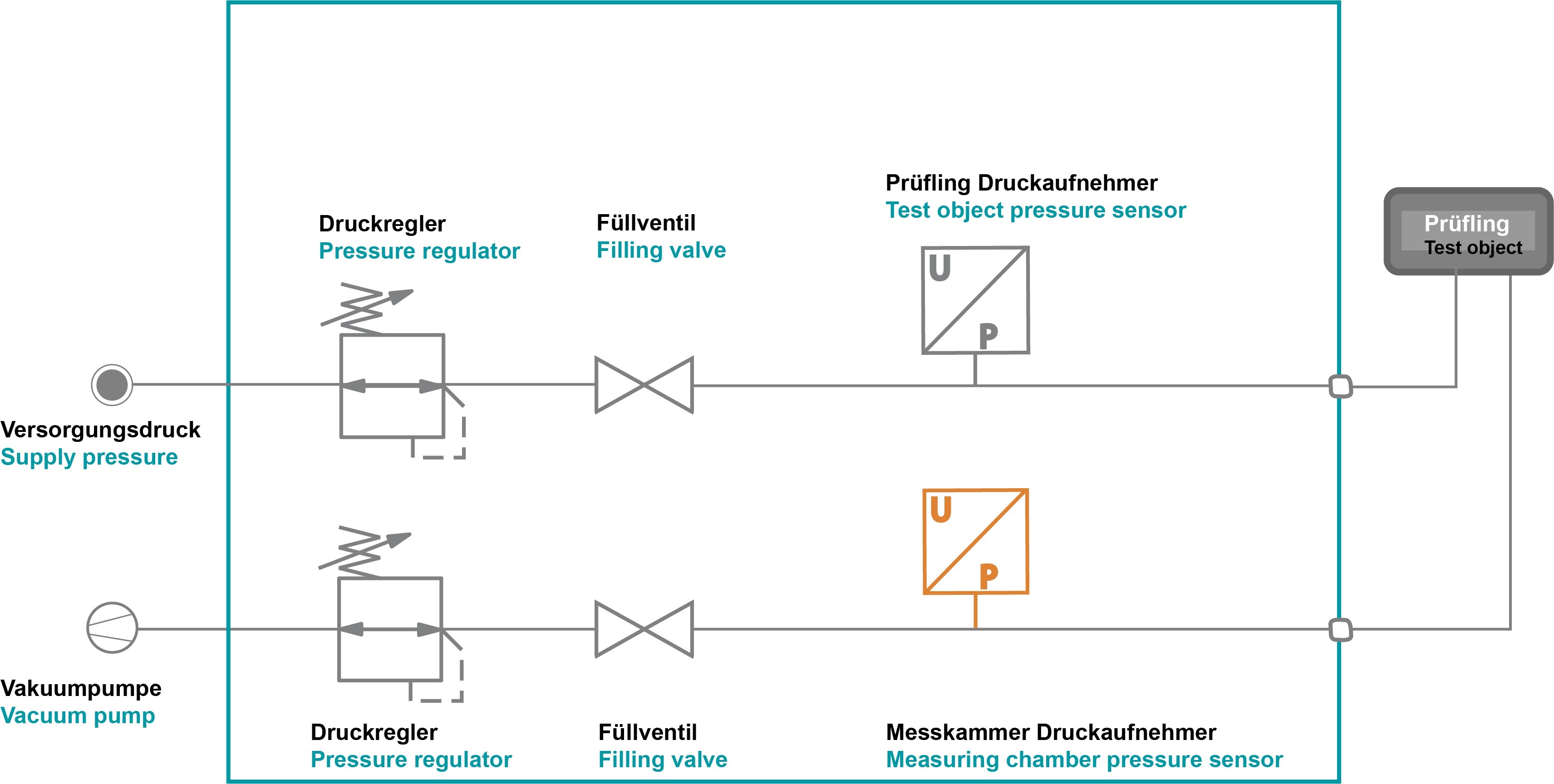
Test medium:
Compressed air/vacuum or nitrogen
Test pressures:
Test pressures up to 1,000 bar possible
Detectable leak rates:
Chamber volume and pressure dependent > 0.1 cm3 / min
Method:
Test item is subjected to pressure / vacuum. The pressure change caused by leakage in a chamber surrounding the test item is measured and evaluated.
Advantages:
- Test pressure can be as high as desired (up to 1,000 bar)
- Very fast test procedure, as there is usually no settling phase
- Small leakage rates up to 0.1 cm3 / min possible
- Worker-independent assessment
- Chamber provides mechanical protection in case of e.g., bursting of the test specimen
Disadvantages:
- Often high mechanical effort due to the use of a volume-optimized test bell
- Test piece and adaptation can only be seen through the test bell to a limited extent or not at all.
- A leaking chamber can lead to incorrect results
- The test chamber can also be subjected to slight overpressure or underpressure in order to detect leaks in the chamber.