Accumulation Trace Gas Leak Testing
The accumulation method using trace gas, usually helium or forming gas (hydrogen/nitrogen mixture), is a good compromise between the highly sensitive vacuum integral method and the cost-effective pressure change methods using air.
In those two measurements, the test part is filled and measured in the same area (e.g., inside the battery housing). With this method, a simple accumulation enclosure is used to form a test space outside the test piece. Inside this enclosure, the increase in trace gas concentration is measured under atmospheric pressure over a period of time x. This allows significantly smaller leaks to be detected.
This makes it possible to detect much smaller leaks than with the pressure change method. The greatest advantage, however, is the independence from environmental influences such as the temperature of the test item or the environment, draughts, vibrations, etc. It allows, for example, leak testing of recently welded or otherwise thermally treated test specimens.
Even test specimens with very large and unstable volumes can be tested quickly and efficiently.
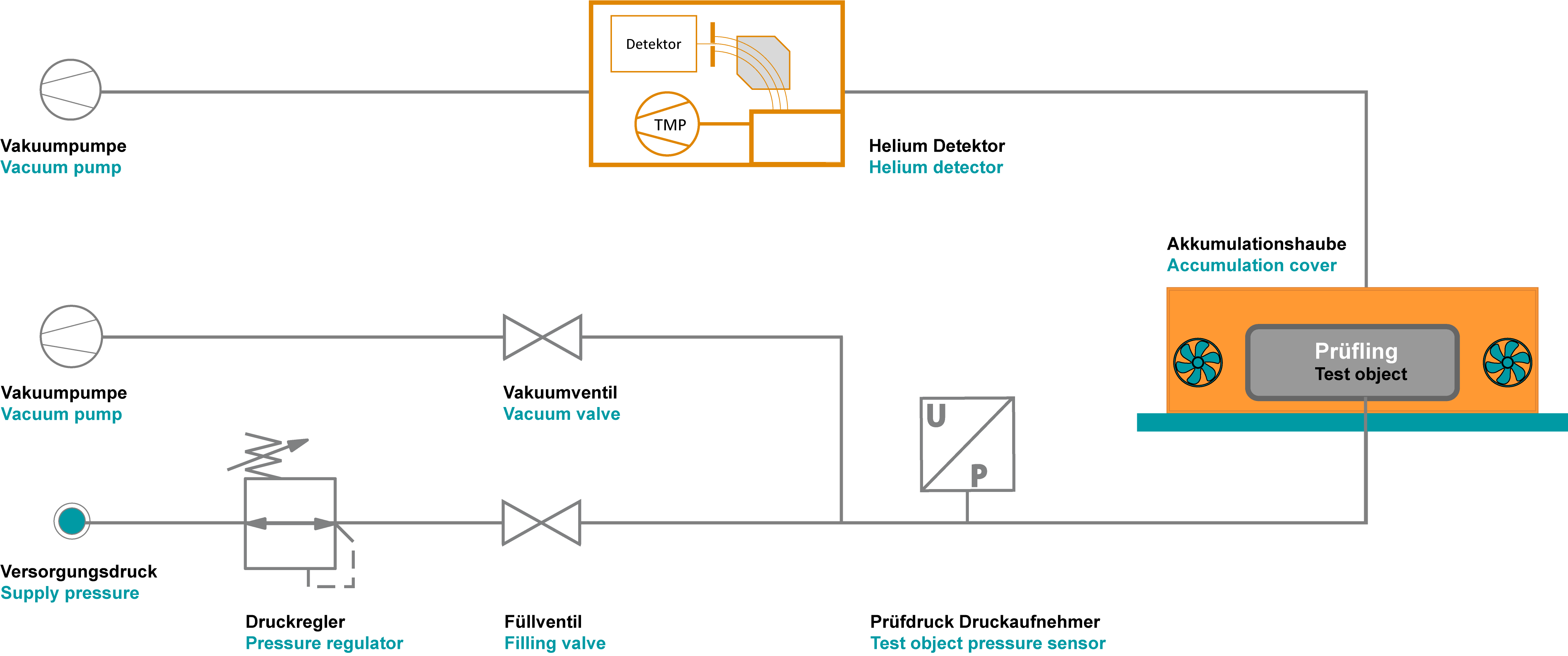
Test medium:
Helium, helium mixture (air or nitrogen), forming gas (5% H / 95% N)
Test pressures:
Stepless from 0.01 - 1,000 bar
Detectable leak rates:
Volume and component dependent < 1 x 10-3 mbar*l/sec (in industrial environment)
Method:
The test item is filled with a trace gas or trace gas mixture and the gas escaping through a possible leakage is evaluated via a leak detector inside the analysis room.
Advantages:
- Medium investment costs
- Complete detection of the total leakage rate
- Not dependent on environmental conditions (temperature, air movement, etc.)
- Not dependent on the stability of the test object (small volume changes, vibrations, etc.)
- Smaller leak rates than can be detected with air
- Partially faster than leak test methods with air
- Worker-independent assessment
Disadvantages:
- Handling of trace gas required
- Higher equipment and test rig costs (compared to air testing)
- Cleaning system for "contaminated environment" required (enclosure venting)